|
It Starts
with the Grain�.
Of
course, grist mills grind of variety of grains, such as
wheat, rye and corn. But in Rhode Island, particularly at
Gray's Mill, native-grown corn, particularly Narragansett
White Flint Corn, was the most common "grist for the mill."
The corn is husked, then dried for six months. It is then
shelled, and packed for grinding. |
|
Into
the Hopper�
|
The
dried, shelled corn is then poured out of the bag, and into
the hopper. The hopper, of course, is the receptacle above
the grinding stone. A vertical rod, called the "damsel,"
is used to shake the kernels downward, through the "shoe"
and onto the millstone. The hopper releases an average of
three bushels of corn an hour for grinding. |
A Word
About the Millstones�
The
two granite millstones at Gray's Mill are 15 inches thick,
and weigh a total of 1 ½ tons. An enormous tonnage,
considering that they were imported from France. Originally,
one stone was used for food, and the other for animal feed.
The
grinding surface of these "runner" stones, or
top stones, is concave and carved in spoke patterns. The
runner stone sits atop another "bed stone" or
"nether stone," which is also carved. As the
top stone rotates, the grain first gets cracks in the
middle of the two stones, then is pushed to the outside
by the spoke-like pattern. The finest grinding occurs
along the perimeter.
When
the millstones need to be cleaned, sharpened or repaired,
the runner stone is lifted with a Stone Crane, using a
pulley.
|
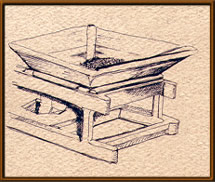 |
Turning
the Stones�
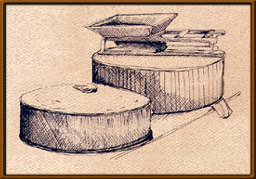 |
Traditionally,
the millstone rotates by waterpower. At Gray's Mill, a Sluice
Gate was used to start and stop the flow of water from the
mill pond across the street. The Sluice Gate is opened by
turning the Sluice Gate Wheel, which starts the flow of
water, causing the water wheel to turn, thus providing power
to grind the grain.
Eventually,
as water levels in the mill pond became unreliable, drying
out during much of the year, water power at Gray's Mill
was supplemented with a 1946 Dodge truck engine from an
old Cain's mayonnaise truck. By 1960, the mill was powered
entirely by this engine.
|
Separating
the Chaff �
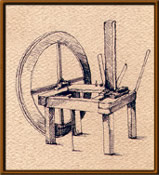 |
As
the ground corn falls from the grain spout, it is filtered
through a mesh screen that sifts out the coarser pieces
of the corn's bran, or outer layers.
These
coarse remains are placed in the "Chaff Bin"
and used for animal feed by local farmers.
|
On to the
Market �
Freshly
ground sacks of corn are then hauled into the bagging room,
where it is weighed on a scale and hand-bagged using a funnel.
Since traditionally milled corn contains none of the preservatives
found in store bought grains, it must be kept refrigerated
to preserve freshness. |
|
|
|